What happens when you 3D-print an elephant and a microlaser inside a living cell?
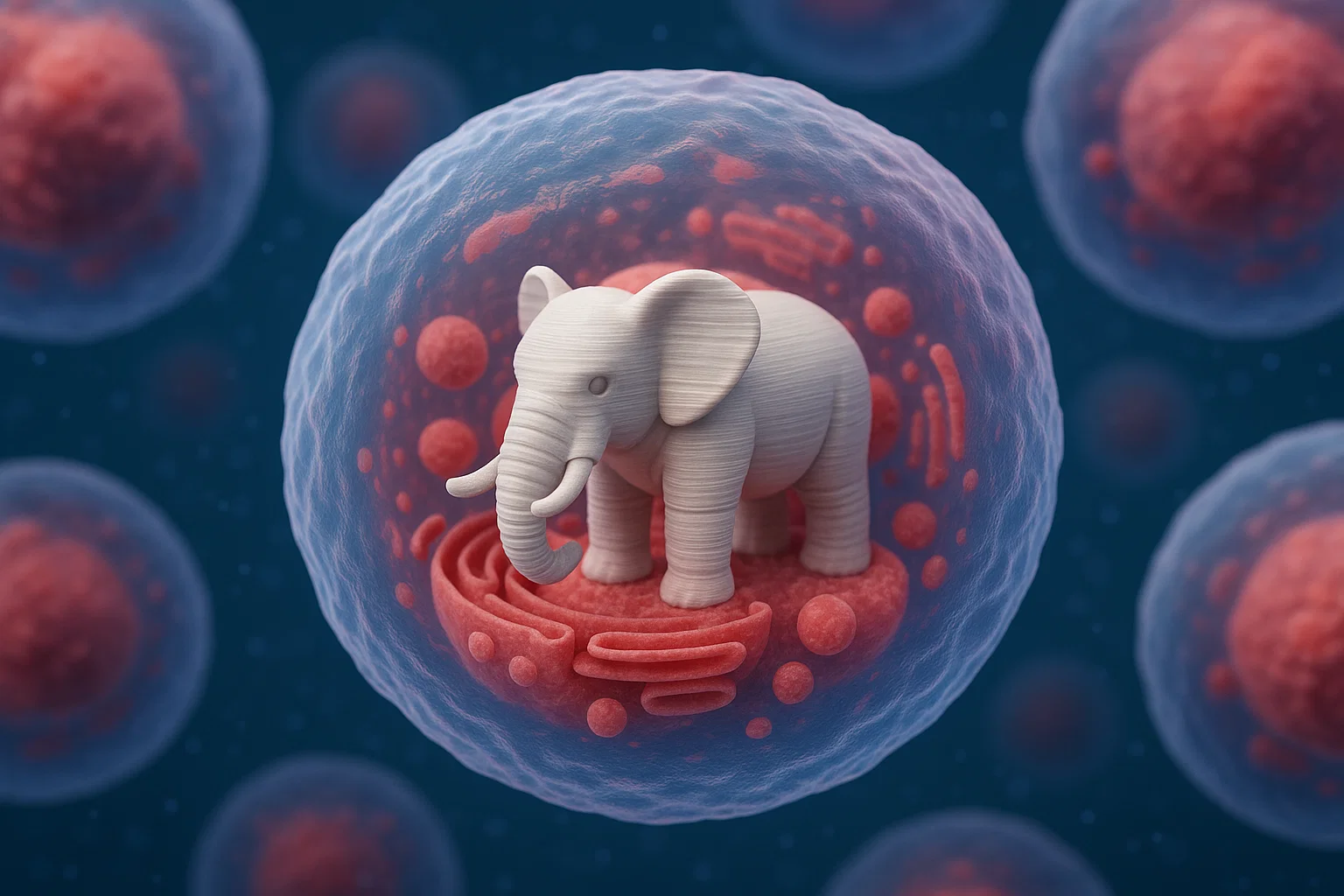
Imagine if doctors could precisely print miniature capsules capable of delivering cells needed for tissue repair exactly where they are needed inside a beating heart. A team of scientists led by Caltech has taken a significant step toward that ultimate goal, having developed a method for 3D printing polymers at specific locations deep within living animals. The technique relies on sound for localization and has already been used to print polymer capsules for selective drug delivery as well as glue-like polymers to seal internal wounds.
(Someone already probably posted this. This is jus from Caltech)
When the team used the DISP platform to print polymers loaded with doxorubicin, a chemotherapeutic drug, near a bladder tumor in mice, they found substantially more tumor cell death for several days as compared to animals that received the drug through direct injection of drug solutions.
“We have already shown in a small animal that we can print drug-loaded hydrogels for tumor treatment,” Gao says. “Our next stage is to try to print in a larger animal model, and hopefully, in the near future, we can evaluate this in humans.”
The team also believes that machine learning can enhance the DISP platform’s ability to precisely locate and apply focused ultrasound. “In the future, with the help of AI, we would like to be able to autonomously trigger high-precision printing within a moving organ such as a beating heart,” Gao says.
Researchers at the University of Colorado Boulder have created a new way to build and control tiny particles that can move and work like microscopic robots, offering a powerful tool with applications in biomedical and environmental research.
The study, published in Nature Communications, describes a new method of fabrication that combines high-precision 3D printing, called two-photon lithography, with a microstenciling technique. The team prints both the particle and its stencil together, then deposits a thin layer of metal—such as gold, platinum or cobalt—through the stencil’s openings. When the stencil is removed, a metal patch remains on the particle.
The particles, invisible to the naked eye, can be made in almost any shape and patterned with surface patches as small as 0.2 microns—more than 500 times thinner than a human hair. The metal patches guide how the particles move when exposed to electric or magnetic fields, or chemical gradients.
By Heidi Hausse & Peden Jones/The ConversationTo think about an artificial limb is to think about a person.
Researchers from the Massachusetts Institute of Technology (MIT) in the United States have created a tiny 3D printer chip-sized device that forms the necessary objects using light in a matter of seconds.
A team of researchers led by Professor Elena Nataros has created a 3D printer that emits a reconfigurable beam of light into resin to create solid forms. This tiny printer fits in the palm of your hand. It is expected that users will be able to quickly create customized, low-cost objects.
According to the developers, the system consists of a single photonic chip measuring a few millimeters, without any additional moving parts. It emits visible light into the resin, allowing for non-mechanical 3D printing.
With the rise of 3D printing and other advanced manufacturing methods, engineers can now build structures that were once impossible to fabricate. An emerging design strategy that takes full advantage of these new capabilities is topology optimization—a computer-driven technique that determines the most effective way to distribute material, leading to an optimized design.
Now, a research team including mathematicians from Brown University has developed a new approach that dramatically improves the speed and stability of topology optimization algorithms. The team, a collaboration between researchers at Brown, Lawrence Livermore National Laboratory and Simula Research Laboratory in Norway, detailed their work in two recently published papers in the SIAM Journal on Optimization and Structural and Multidisciplinary Optimization.
“Our method beats some existing methods by four or five times in terms of efficiency,” said Brendan Keith, an assistant professor of applied mathematics at Brown. “That’s a huge computational savings that could enable people to make designs more quickly and inexpensively, or to develop more complex designs with higher resolution.”
Lawrence Livermore National Laboratory (LLNL) researchers have developed a novel 3D printing technique that uses light to build complex structures, then cleanly dissolves the support material, expanding possibilities in multi-material additive manufacturing (AM).
In 3D printing, traditional supports often add time, waste and risk to the process, especially when printing intricate parts. But in a new study published in ACS Central Science, an LLNL team—in collaboration with University of California, Santa Barbara (UCSB) researchers—outlines a “one-pot” printing approach that uses two light wavelengths to simultaneously create permanent structures and temporary supports from a single resin formulation.
The method addresses a longstanding challenge in AM: how to fabricate suspended or overhanging features without cumbersome scaffolding requiring manual removal, which is a key hurdle to the widespread adoption of digital light processing (DLP) 3D printing technologies.